What are the Quality Assurance Benchmarks (QABs)?
GIA’s Quality Assurance Benchmarks are developed with support and feedback from the jewelry industry to:
- Provide an objective method for evaluating the quality of semi- or fully finished jewelry by comparing it against acknowledged criteria.
- Enhance customer relationships by ensuring production and presentation of quality products.
- Increase customer understanding and appreciation of the jewelry’s unique qualities and value, resulting in greater sell-through.
- Demonstrate methods for achieving quality.
- Offer a general range of information about the unique characteristics of working with specific metals for post-sale service and alterations.
WHY ARE THE QABs SO IMPORTANT?
Quality Assurance Benchmarks were developed as a means to easily identify criteria of poor workmanship or other factors that would cause jewelry failure after purchase.
Types of jewelry failure include:
- Lost diamonds or stones.
- Shape distortion from normal wear.
- Damage to gemstones, jewelry structure, or finish.
Reasons for failure that can be avoided include:
- Errors in workmanship.
- Use of the wrong materials.
- Poor design or product engineering.
For retailers, consequences of jewelry failure include:
- Stressful encounters with customers.
- Loss of confidence in your business and, ultimately, the industry.
- Financial loss due to probable replacement, time lost in remaking, and loss of customers.
- Loss of future jewelry sales.
CONTENTS OF THE QABs
Each interactive benchmark includes Quality Assurance Benchmarks for specific situations, such as ring sizing. Benchmarks also include a description of potential problems or engineering features. Many benchmarks include short two to four minute videos that demonstrate specific manufacturing techniques. These how-to videos:
- Help prevent jewelry failure during normal wear.
- Introduce the workmanship basics of repairing or altering jewelry at the bench.
- Provide a consistent model for shop staff training.
- Increase understanding and appreciation for an alloy’s unique qualities among retail store owners, buyers, sales professionals, and consumers.
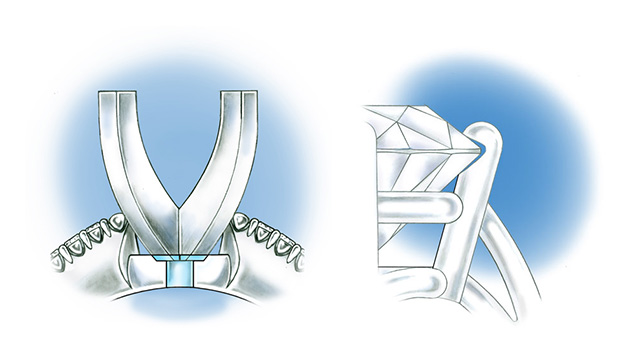
Illustrations like these provide examples of real jewelry to evaluate the quality of jewelry.
Benchmarks also contain relevant general information, including:- Shop tips.
- Tool recommendations or modifications.
- Safety tips.
- Sales assistance.
- Best practices.
WHO ARE THE QABs FOR?
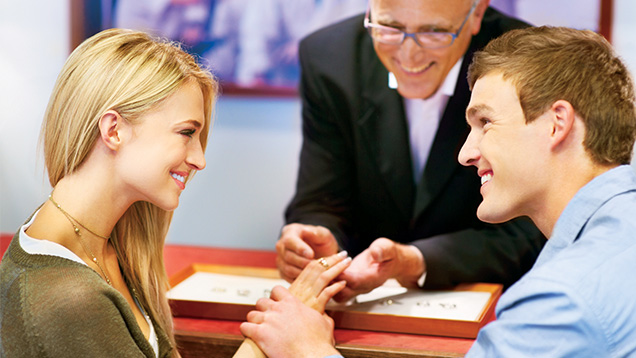
Quality Assurance Benchmarks are vital to anyone concerned with jewelry, including bench jewelers, retail sales professionals and shop managers/owners, jewelry consumers, buyers, manufacturers, and designers.
Bench jewelers
Knowing about quality criteria enhances a bench jeweler’s performance and team communication. Understanding Quality Assurance Benchmarks is vital to bench jewelers in order to:
- Understand the difference between jewelry alloys.
- Accurately advise customers on post-sale jewelry repairs or alterations.
- Effectively repair, set, or alter jewelry.
- Avoid costs due to returns, damage to jewelry, or stone loss.
Retail Sales Associates
Familiarity with Quality Assurance Benchmarks enables retail sales associates to:
- Effectively compare jewelry metals.
- Increase customer awareness and appreciation of jewelry alloys, resulting in greater sell-through.
- Effectively examine jewelry when taking it in for repair or alteration.
- Accurately advise customers on jewelry repairs or alterations.
Retail Shop Managers and Owners
For retail shop managers and store managers or owners, understanding Quality Assurance Benchmarks:
- Provides an objective means of communicating quality with manufacturers and suppliers.
- Provides an objective method of comparing product quality between manufacturers.
- Provides a standard for evaluating metal-working skills of bench jewelers.
- Reduces cost of returns and replacements due to product failure.
- Improves customer relationships through reduced incidence of product failure.
Customers
Customers who understand Quality Assurance Benchmarks:
- Tend to engage in comparison shopping for quality and not just price point.
- Better appreciate the exceptional qualities of specific alloys.
- Are better able to care for jewelry.
Manufacturers
For manufacturers, improved jewelry manufacturing standards through Quality Assurance Benchmarking:
- Pinpoint manufacturing processes that contribute to failure.
- Prevent post-sale failure by setting parameters for criteria such as ring mounting and setting .
- Enable in-house quality evaluation, customizable to specific needs.
Jewelry Buyers
For buyers, an understanding of Quality Assurance Benchmarks:
- Provides an objective way to communicate quality with manufacturers and suppliers.
- Provides an objective way to compare product quality between manufacturers.
- Reduces cost of returns and replacements due to product failure.
- Improves customer perception of retail store brand and integrity.
Designers
By referring to Quality Assurance Benchmarks from the start, designers:
- Improve CAD layout and design engineering.
- Build in factors that prevent post-sale jewelry failure.
- Ensure consistent brand quality and integrity.
HOW TO NAVIGATE THE QABs
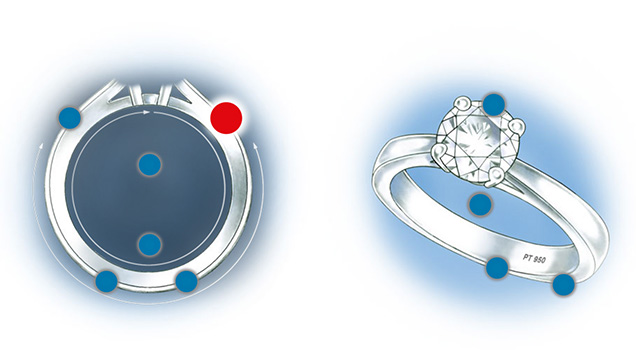
The QAB content for platinum jewelry is organized into four categories representing common functions in jewelry manufacturing: Ring Sizing, Finishing & Polishing, Assembly & Setting, and Tools & Metal Identification. Within each of these categories are detailed pages covering a variety of topics. Each page is organized into sections that contain illustrations, photographs or a how-to video. Illustrations and photographs provide detailed information using beacons. The active beacon will always be red, and you can click through the blue beacons to learn more about that particular item.